Metal 3D Printing (Metal Additive Manufacturing)
In cooperation with multiple players (architects, manufacturers, producers) and a worlwide research and industrial network, Dr. Kanyilmaz has been studying new tubular joint shapes using metal 3D printing to maximize the structural performance and minimize fabrication complexity to reduce costs, increase customization and cut waste as well as the carbon footprint of the AEC industry. He is currently coordinating the EU-funded research project ConstructAdd.
More details can be read in these articles:
Alessandro Menghini, Simone Maffia, Ali Gökhan Demir, Alper Kanyilmaz, Filippo Berto, Carlo Andrea Castiglioni, Barbara Previtali, Performance of laser metal deposition on hot-rolled stainless steel for hybrid steel structures, Construction and Building Materials, Volume 443, 2024, https://doi.org/10.1016/j.conbuildmat.2024.137744.
Kanyilmaz A, Ali Gökhan Demir, Martina Chierici, Filippo Berto, Leroy Gardner, Sastry Yagnanna Kandukuri, Paul Kassabian, Takuya Kinoshita, Andrea Laurenti, Ingrid Paoletti, Anton du Plessis, Seyed Mohammad Javad Razavi, Role of metal 3D printing to increase quality and resource-efficiency in the construction sector, Additive Manufacturing, Volume 50, 2022, 102541, ISSN 2214-8604, https://doi.org/10.1016/j.addma.2021.102541
Kanyilmaz, A., Berto, F., Paoletti I., Caringal, R.J., Mora, S., Nature-inspired optimization of tubular joints for metal 3D printing, Struct Multidisc Optim (2020). https://doi.org/10.1007/s00158-020-02729-7, Springer Nature
Chierici, M., Demir, A.G., Kanyilmaz, A., Berto F., Castiglioni, C.A, Previtali B.,. Hybrid manufacturing of steel construction parts via arc welding of LPBF-produced and hot-rolled stainless steels. Prog Addit Manuf (2023). https://doi.org/10.1007/s40964-023-00466-z
Steel joint fabrication using laser cutting
Dr. Kanyilmaz and his team are at the forefront of innovating tubular steel structure joints through Laser Cutting Technology (LCT), aiming to enhance steel construction by leveraging the exceptional structural and aesthetic qualities of steel hollow sections. He has been coordinating the EU-funded research project LASTTS, where a large multi-national and interdisciplinary team has been testing the essential tubular joint components to contribute to the development of a new, comprehensive experimental database.
Up to day, 36 two-way steel joints have been tested under monotonic gravity, opposite bending and shear loading conditions. The new joint configurations performed better than the conventional tubular joint options with up to 2.5 times more resistance and 10 times more stiffness. The superior structural performance translated in significant economic and environmental benefits (up to 35% saving in steel frame costs).

More details can be read in these articles:
Mouad Madhouni, Maël Couchaux, Mohammed Hjiaj, Alper Kanyilmaz, Passing-through I-plates-to-SHS moment resisting joints subjected to symmetric bending moments, Thin-Walled Structures, 2024, 112442, ISSN 0263-8231, https://doi.org/10.1016/j.tws.2024.112442
Couchaux M., Vyhlas V., Kanyilmaz A., Hjiaj M., Passing-through I-beam-to-CHS column joints made by laser cutting technology: Experimental tests and design model, Journal of Constructional Steel Research, Volume 176, 2021, 106298, ISSN 0143-974X, https://doi.org/10.1016/j.jcsr.2020.106298
Das R., Kanyilmaz A., Couchaux M., Hoffmeister B., Degee H., Characterization of moment resisting I-beam to circular hollow section column connections resorting to passing-through plates, Engineering Structures, Volume 210, 2020, 110356, ISSN 0141-0296, https://doi.org/10.1016/j.engstruct.2020.110356
Kanyilmaz, A., Castiglioni C.A., Fabrication of laser cut I-beam-to-CHS-column steel joints with minimized welding, Journal of Constructional Steel Research, Volume 146, 2018, Pages 16-32, ISSN 0143-974X, https://doi.org/10.1016/j.jcsr.2018.02.039
Kanyilmaz, A., The problematic nature of steel hollow section joint fabrication, and a remedy using laser cutting technology: A review of research, applications, opportunities, Engineering Structures, Volume 183, 2019, Pages 1027-1048, ISSN 0141-0296, https://doi.org/10.1016/j.engstruct.2018.12.080
Menghini A., Kanyilmaz A., Calado L., Castiglioni C.A., Experimental Assessment of the Behavior of Tubular Truss Girder Joints Fabricated with Laser Cutting Technology (2023) Journal of Structural Engineering (United States), 149 (6), https://doi.org/10.1061/JSENDH.STENG-12019
Related news
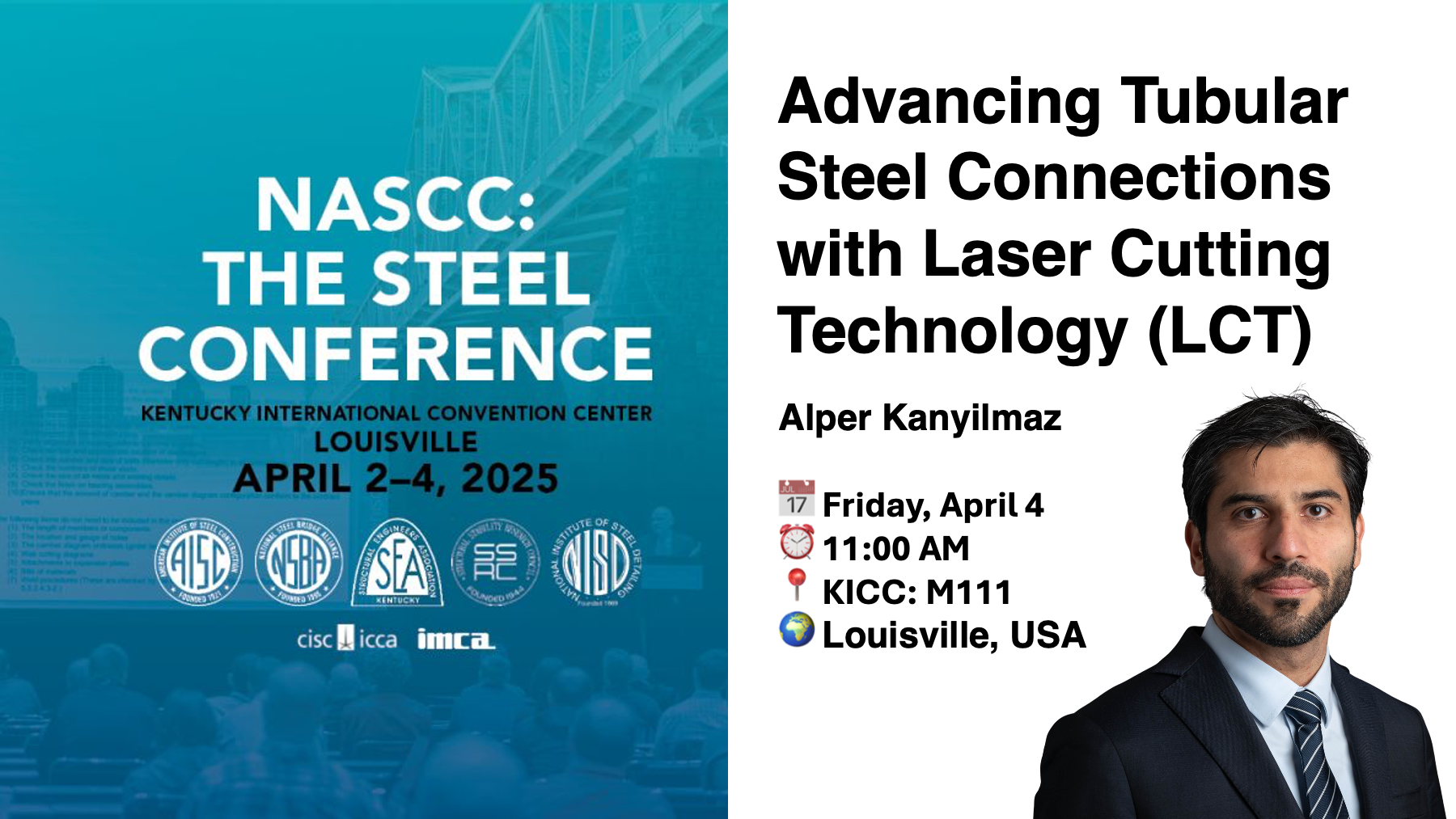
Next-Generation Fabrication: Laser Cutting for Tubular Steel Connections at NASCC 2025
4 April 2025
In NASCC 2025, Lousville, USA, Alper Kanyilmaz will talk about the use of Laser Cutting Technology
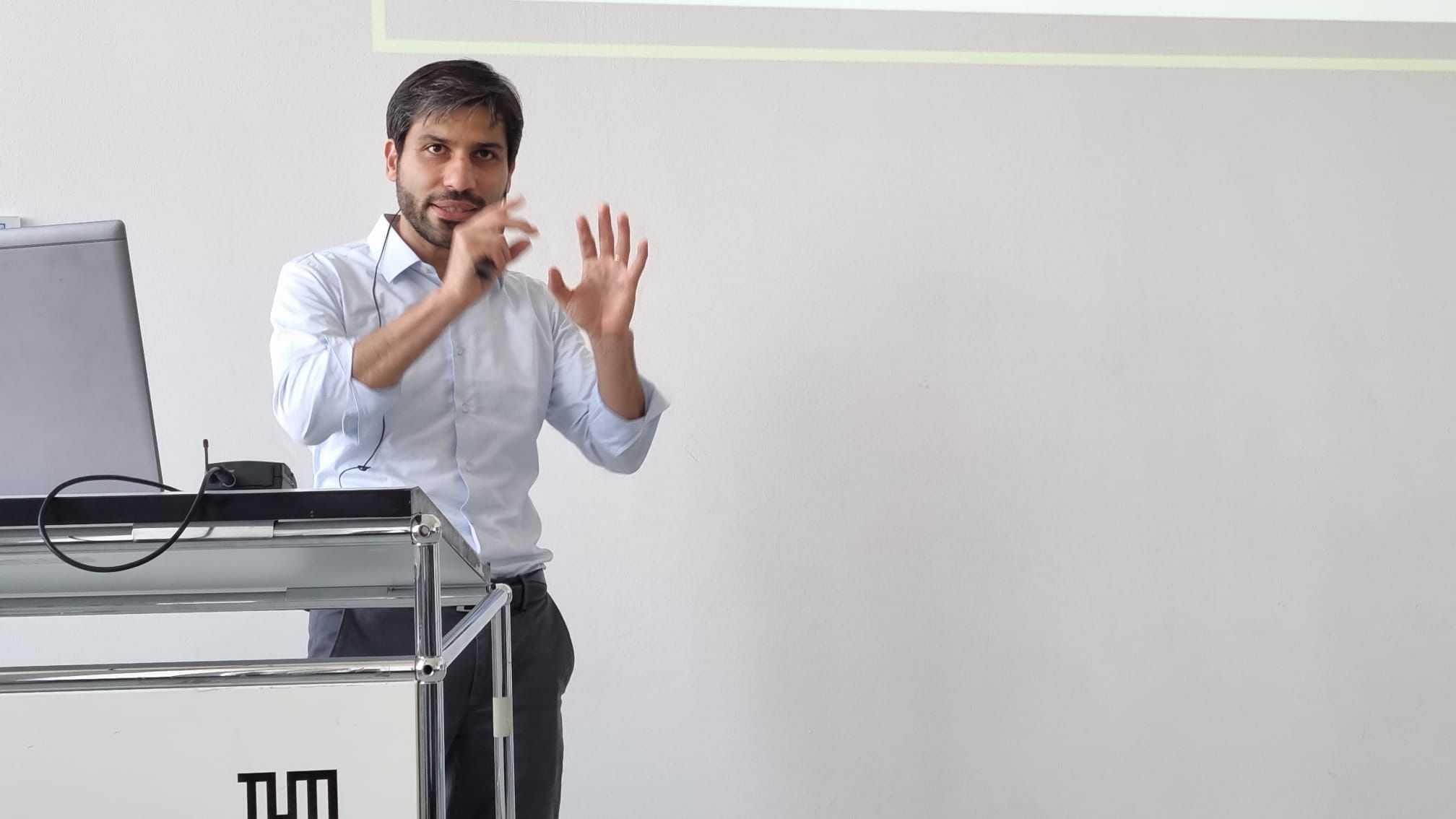
Visiting research in Technical University of Munich, Germany
10 July 2024
Alper Kanyilmaz visited Prof. Martin Mensinger at his Metal Structures chair at the Technical University of Munich,
… Continue reading Visiting research in Technical University of Munich, Germany
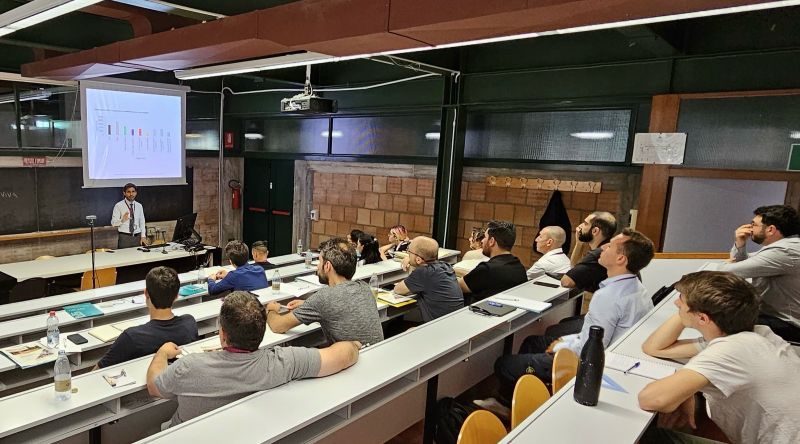
Lecture in Bologna, Italy
8 July 2024
Alper Kanyilmaz gave a lecture with title “Life cycle driven strategies for large-scale metal 3D printing” in
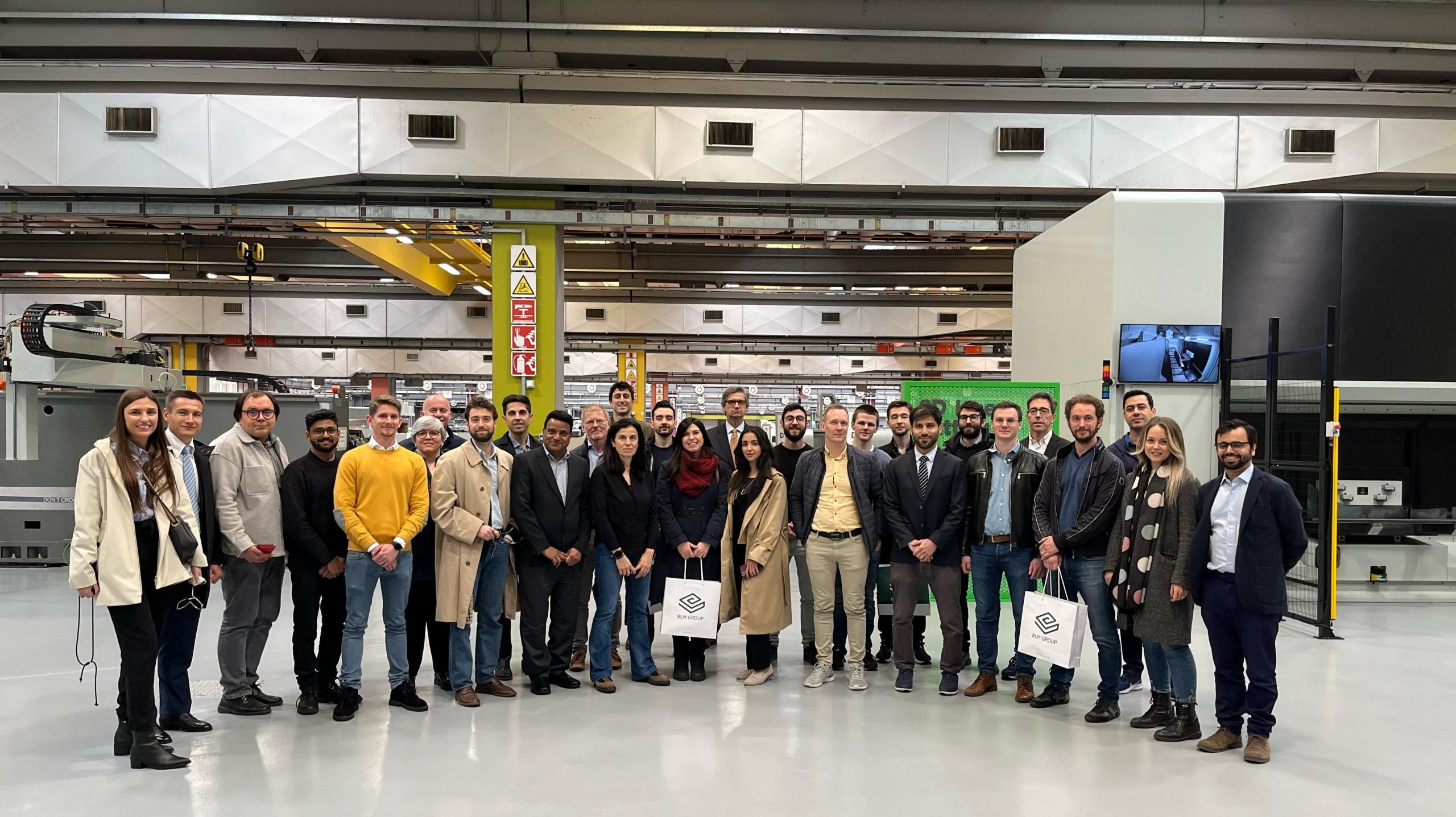
ConstructAdd team is growing.
10 April 2024
Beyond dreaming, the EU-funded R&D project ConstructAdd is making steps toward a future
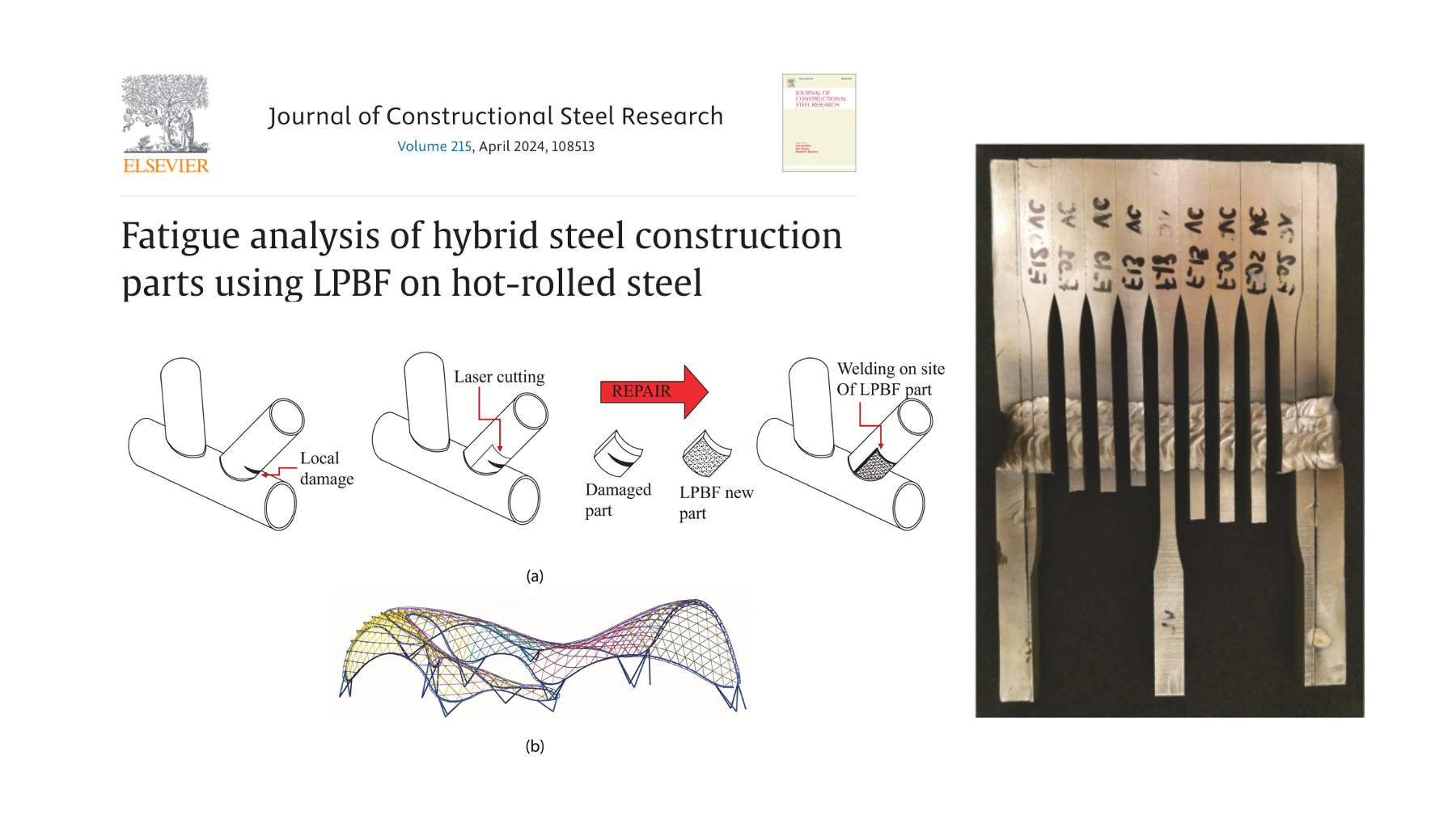
New article “Fatigue analysis of hybrid steel construction parts using LPBF on hot-rolled steel”
8 February 2024
In his recent article, Dr. Kanyilmaz and his colleagues looked into the ways
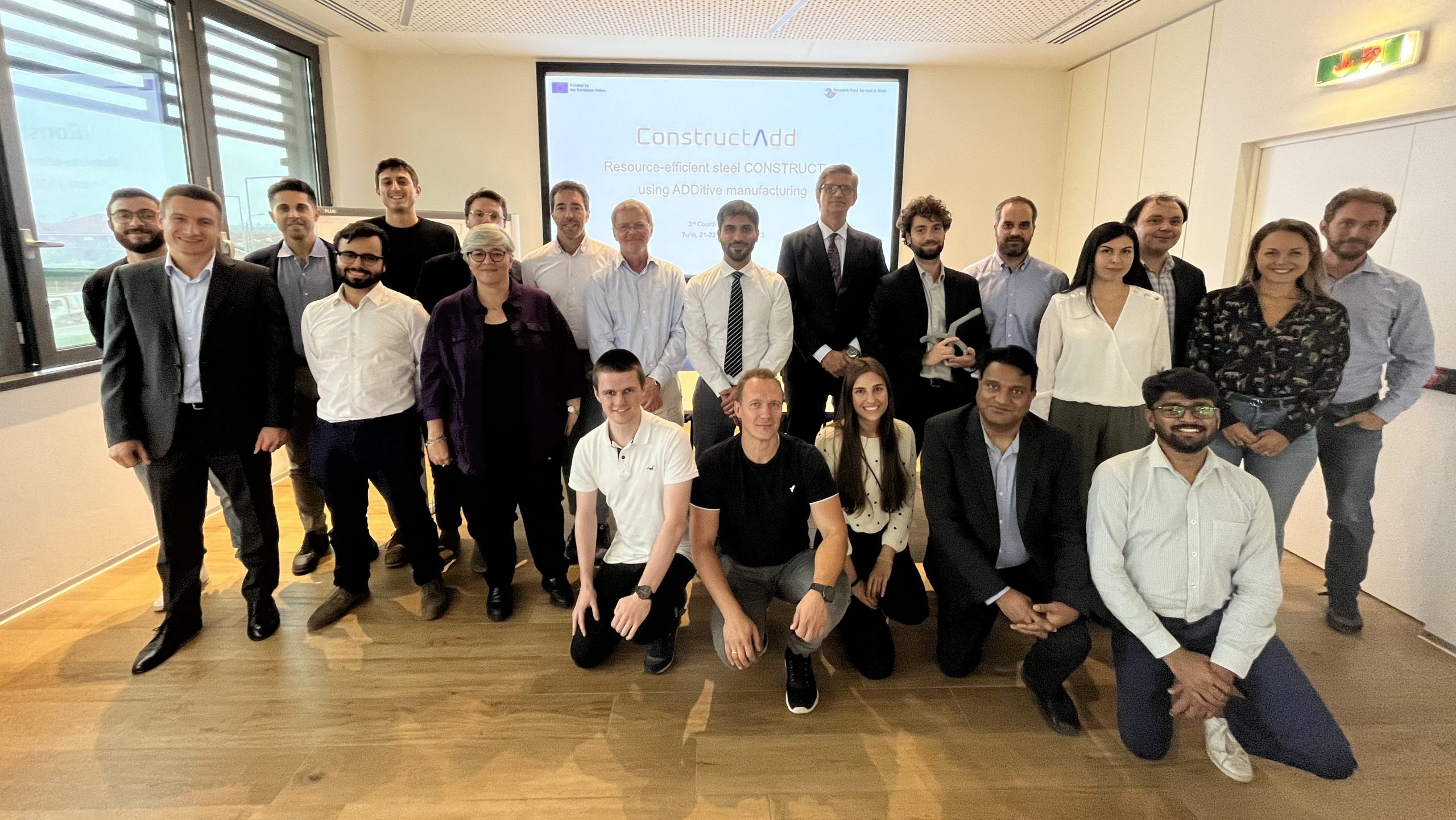
3rd coordination meeting of ConstructAdd project
21-22 September 2023
3rd coordination meeting of ConstructAdd project took place in Turin, Italy. ConstructAdd is a EU-RFCS project coordinated
… Continue reading 3rd coordination meeting of ConstructAdd project
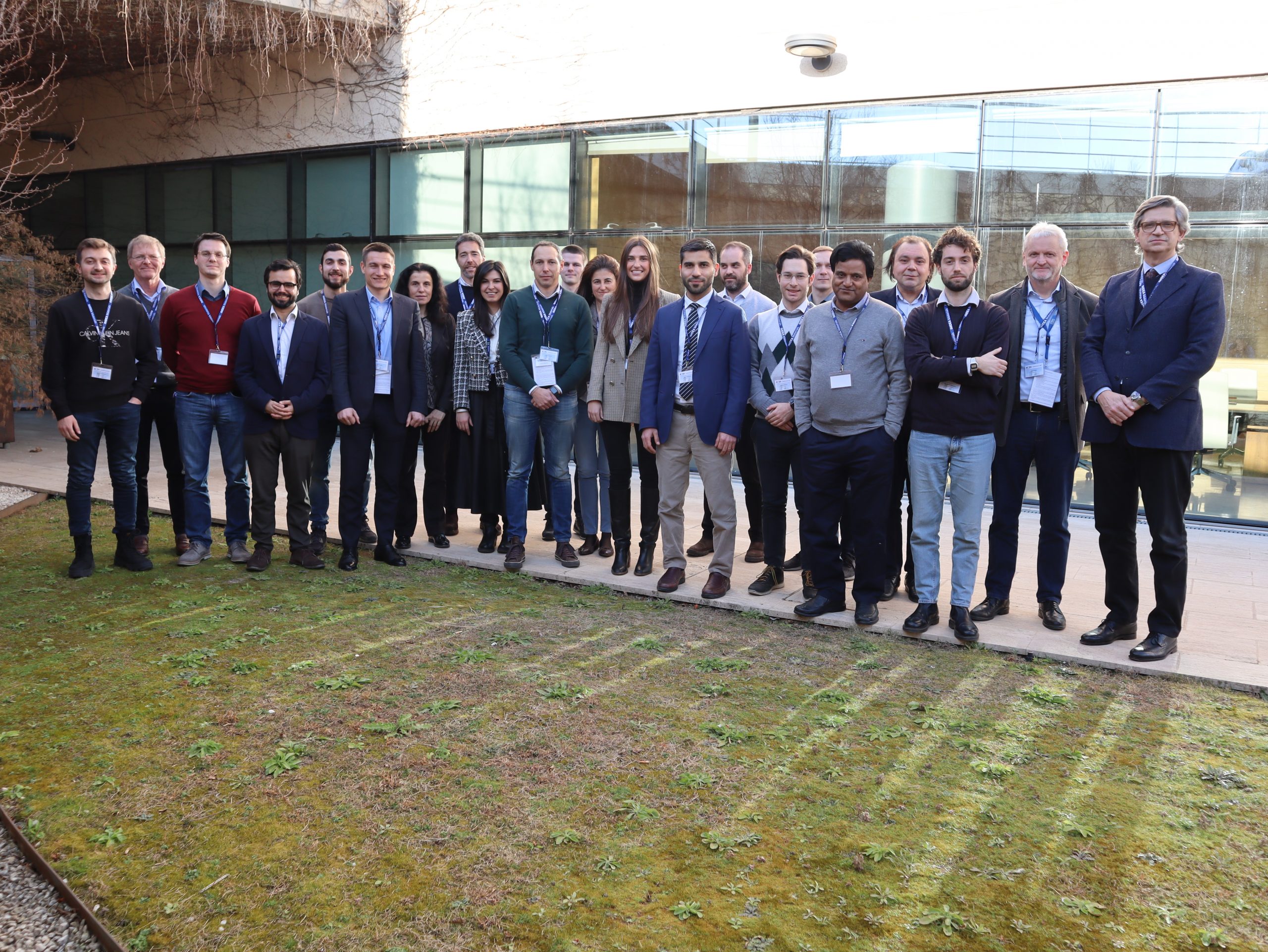
ConstructAdd 2nd coordination meeting in Madrid
9 February 2023
ConstructAdd 2nd coordination meeting in Madrid took place in Madrid, Spain.
Project coordinator Alper Kanyilmaz from
… Continue reading ConstructAdd 2nd coordination meeting in Madrid
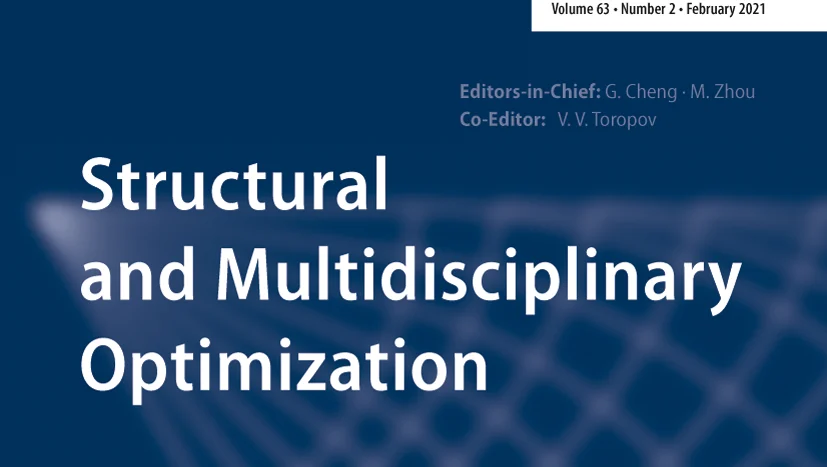
Nature-inspired optimization of tubular joints for metal 3D printing
1 August 2021
New article published: “Nature-inspired optimization of tubular joints for metal 3D printing”. We analyzed new tubular joint
… Continue reading Nature-inspired optimization of tubular joints for metal 3D printing
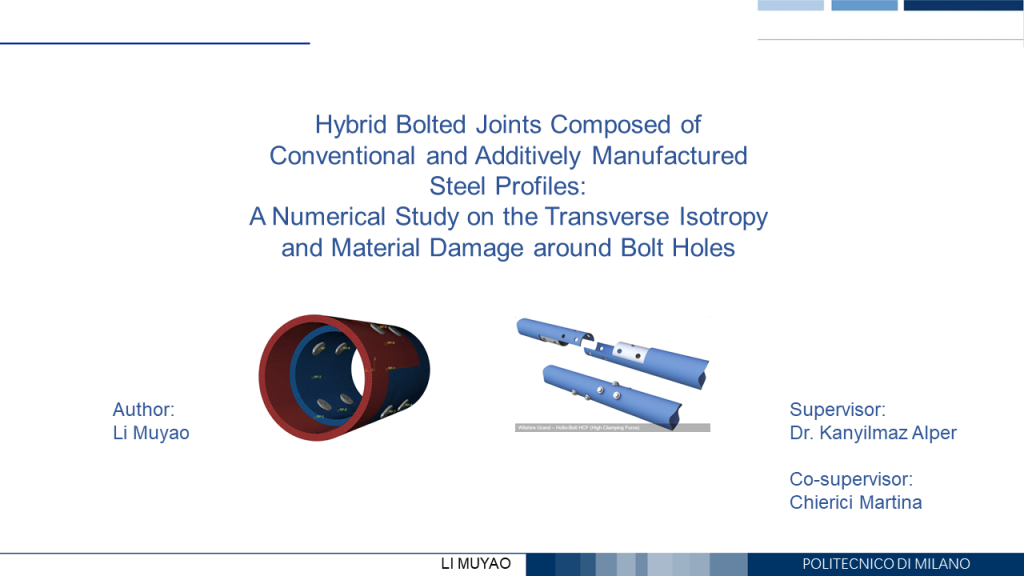
Hybrid bolted joints composed of conventional and additively manufacturated steel profiles
22 July 2021
Our MSc student Muyao Li discussed successfully his thesis